Modtec Story
Established and Incorporated in May 1969
1969
- Purchased by Bruce Davies and Allan Harrison in approx. 1969 as a fence stain manufacturing business.
- An engineering partnership of 4 was started in to set up a Zinc diecasting business to manufacture toys.
- Modtec was one of the first Companies in NZ to use tangential runner technology established by CSIRO 1979/80. Early adopter of oil hydraulic diecasting technology.
1981
- All the assets and the business of the engineering partnership was purchased by Modtec Industries Ltd.
- Modtec established a contracting Zinc Diecasting business.
- Modtec established a tool room to enable experimentation and innovation.
1982
- Modtec convened a day conference with Independent CSIRO advisor and NZ diecasting casting producers to improve the performance in the industry.
1983
- Further invested assets to develop NZ diecasting machines and other assets to build the business.
- Zinc diecasting supplier to many local companies.
1985
- Modtec began exporting zinc castings to Australian customers.
- Modtec added a large British and European office screen manufacturer as a contract customer.
- Modtec became a specialised designer and supplier of zinc diecasting components for aluminium extrusions in the NZ and Australian commercial furniture market.
1987
Innovation in design in Zinc Diecasting
- Modtec developed, designed and implemented modular unit die systems to enable multiple different customers components to be manufactured at the same time with single cavity tooling.
- One of the first companies to eliminate trimming presses in Diecasting.
1990
Electrical Fence and Security business
- Modtec developed into the electrical fence and security business with large NZ exporters.
- Modtec became the supplier to most of the companies in NZ. Modtec added a large USA company and 2 small Australian companies as contract customers.
1994
Modtec Powder coating and Tube Products
- Modtec purchased the assets to be in the powder coating and welded steel ERW tube manufacturing business.
1995
Road Transport recyclable collapsible containers
- The purchase of assets enabled Modtec to innovate, design and manufacture solutions with recycled packaging for the NZ courier and line haul industry in NZ.
- Modtec designed and originated steel collapsible bulk containers for road transport in NZ for NZ Post, Freightways, NZ Couriers, Fastways, PBT and others. This hub and spoke system required designing and building roll cages that were safe, optimised space for sorting line haul volumes in the main city centres for distribution by couriers.
- Modtec partnered with CHEP and began getting insights from companies in the freight industry to consider an industry initiative to develop some standardisation in the market.
1997
- Modtec purchased new assets – Robotic welders, spark erosion, CNC machines etc.
- Created an in-house design team using CAD CAM technology to build these containers.
1999
NZ and Australian Commercial office market
- As globalisation continued the commercial office manufacturing industry in NZ and Australia has made significant changes to importing finished product.
- Modtec had good relationships in the industry and was asked by customers to provide adjustable systems for desks and workstations.
- Modtec realised the need to innovate and develop its own proprietary products due to globalisation.
2002
Homecare Adjustable Beds
- Fisher and Paykel sold their ride on scooter business to an Australian company and suggested their buyer make contact with Modtec. Modtec supported them which led into the design and manufacture of medical beds for home care.
- Export these products to Australia.
- Build a small business in NZ in health and wellbeing by providing individual solutions for home care for the elderly, sick and the injured by designing, manufacturing and supplying the rehabilitation equipment for home.
2003
Start of Apollo monitor arm system
- Modtec visited a customer in England and they asked if we could design and manufacture computer monitor arms.
- Partnership together including an industrial designer, an office furniture supplier and Modtec to design a computer monitor arm.
- This system is still adding innovative solutions to improve Ergonomics and Productivity in the Workspace.
2004
- Launched first version of Apollo at Orgatec in Germany.
- Awarded Auckland exporting award.
- Began selecting suppliers in India for manufacturing of the Apollo series.
2005
Development of Apollo profiles
- Developed wall mounted solutions.
- Pole profiles can be flat or circular: Apollo1, Apollo2 wall, Apollo2, Apollo4.
- Poles can be hollow: Apollo4 Power+, Apollo6.
- Launched Apollo in the USA with Workrite.
2006 - 2007
- Many new entrants to the monitor arm market.
- Developed screen mounted solutions.
- Decision to build a sales organisation and get deeper market insights.
2008
- Sales and Marketing person joined Modtec. Started recruiting BDM’s in Australia and NZ.
- Kimball in the USA became a distributor.
- Modtec manufacturing matrix was introduced.
- Modtec introduced power and data into monitor arm posts.
2009
- More resources were invested into R&D.
- Awarded Innovator of the year with the NZ India Business Council.
- New electrical solutions for monitor mounts were developed.
- Research into entry level monitor mounts.
- Awarded best use of design in international business in all categories by NZ Trade and Industry.
- Introduced power/data floor to ceiling solutions into banks with Apollo6.
2010
- Won 2 further design awards from the Institute of Design and Westpac.
- Invited by NZTE/Better by Design to Silicon Valley USA to visit fast growing global companies and learn insights about the importance and significance of design.
2011
- Began a relationship with Blender Design.
- Introduced LEAN to Modtec. Became a LEAN engagement company.
- Began recruiting and setting-up BDMs in India and Asia.
- Developed concepts, tested many ideas and market insights for a new entry level monitor arm solution.
2012
- Introduced solutions for control rooms.
- Developed BladeRunner dynamic solution for Apollo.
- Developed multiscreen wall mounted or freestanding electric activated power post.
- Began the design process of designing an entry level monitor arm.
2013 -2015
- Developed solutions for laptops and medical accessories.
- Developed further solutions for homecare beds and chair accessories.
- Developed solutions for cable management.
2013 - 2015
- Developed and launched a new electrical power pod “ChargeUp”, a fast charge solution with USB and USB C and 2 NZ/AUS GPO.
- Developed BDM communication app and knowledge bank tools.
- Developed hybrid solution for using Apollo and Array on Sit Stand applications.
2019 - 2021
- Start developing concepts for a new dynamic monitor mount limb for the Apollo series.
- Closed Modtec diecasting operations.
- Setup distribution centres in NZ, Australia and India.
- Launched A20 in NZ, Australia and India.
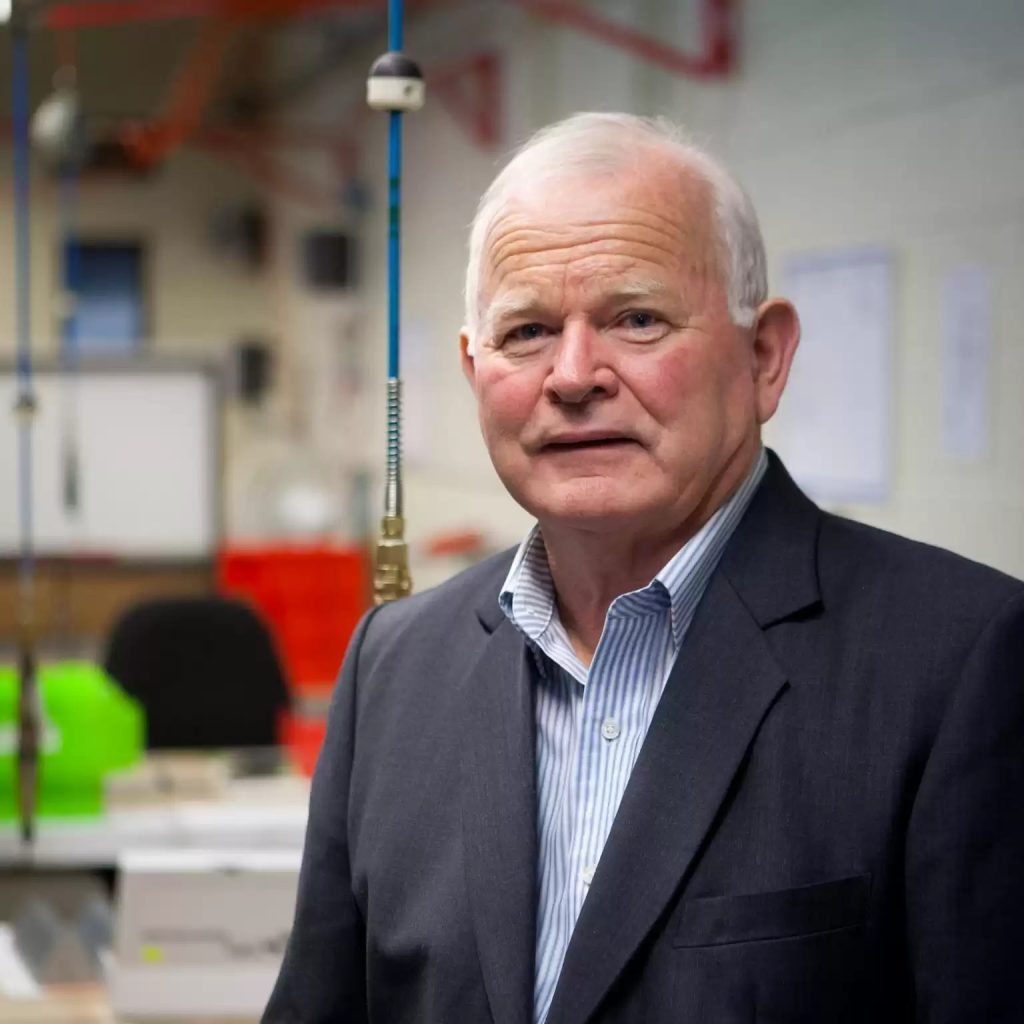
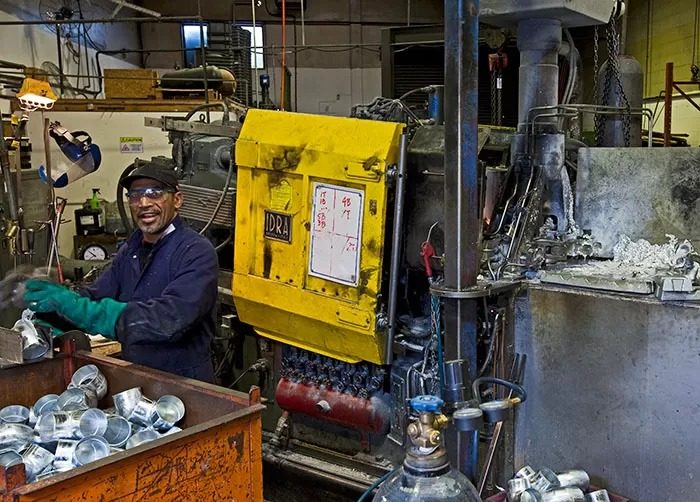
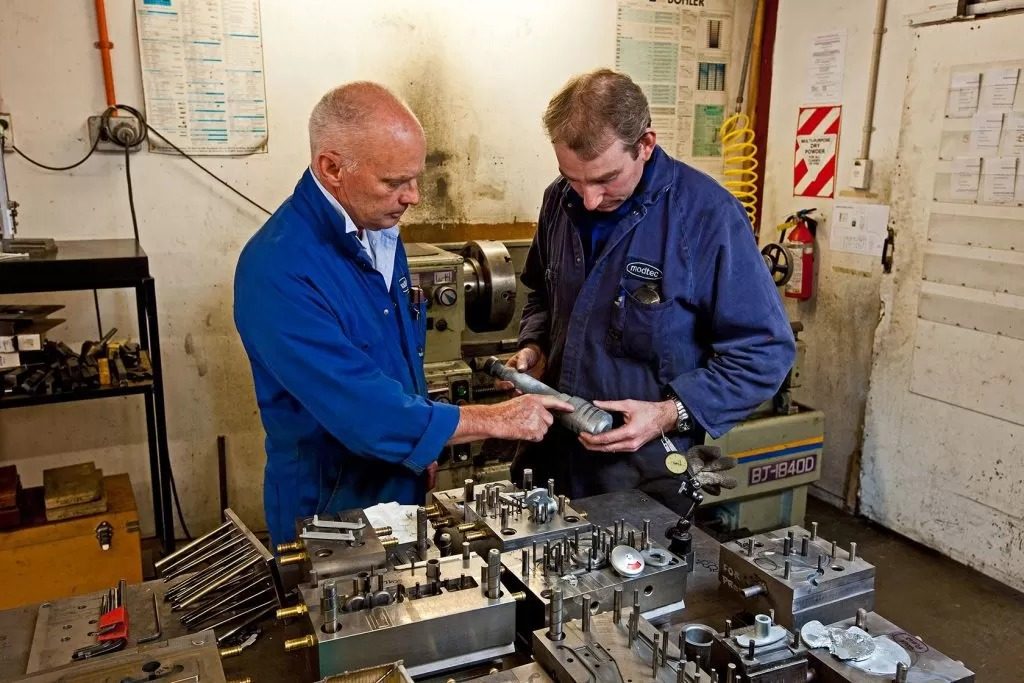
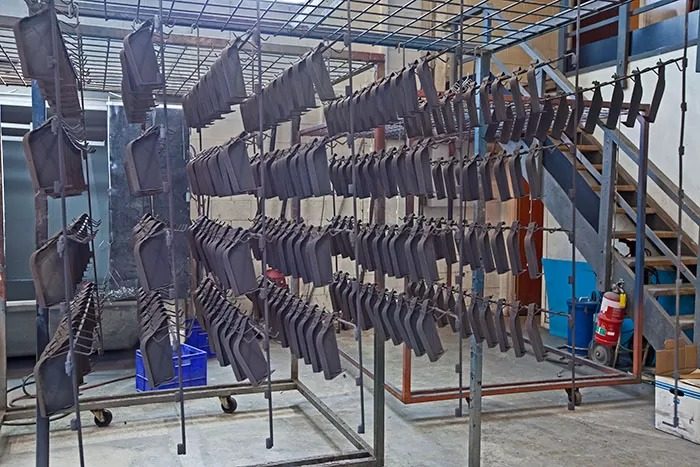
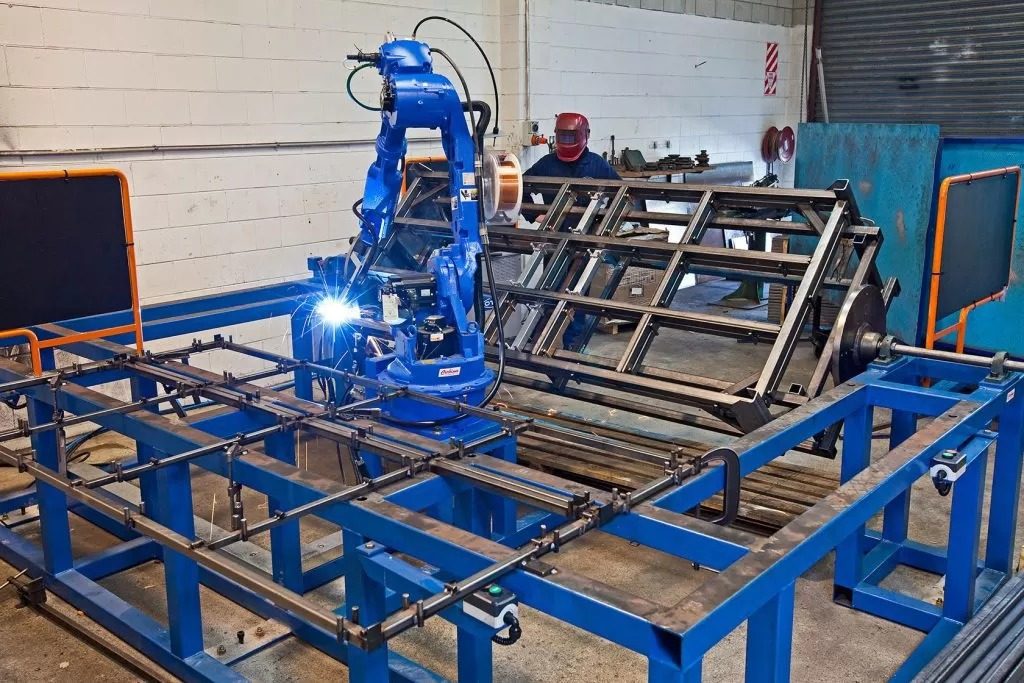
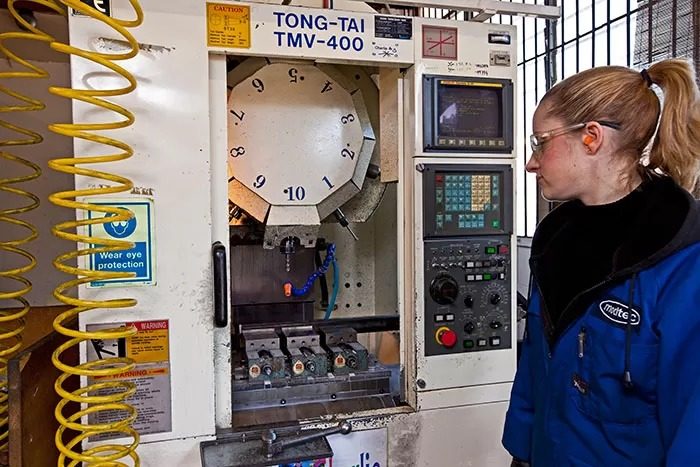
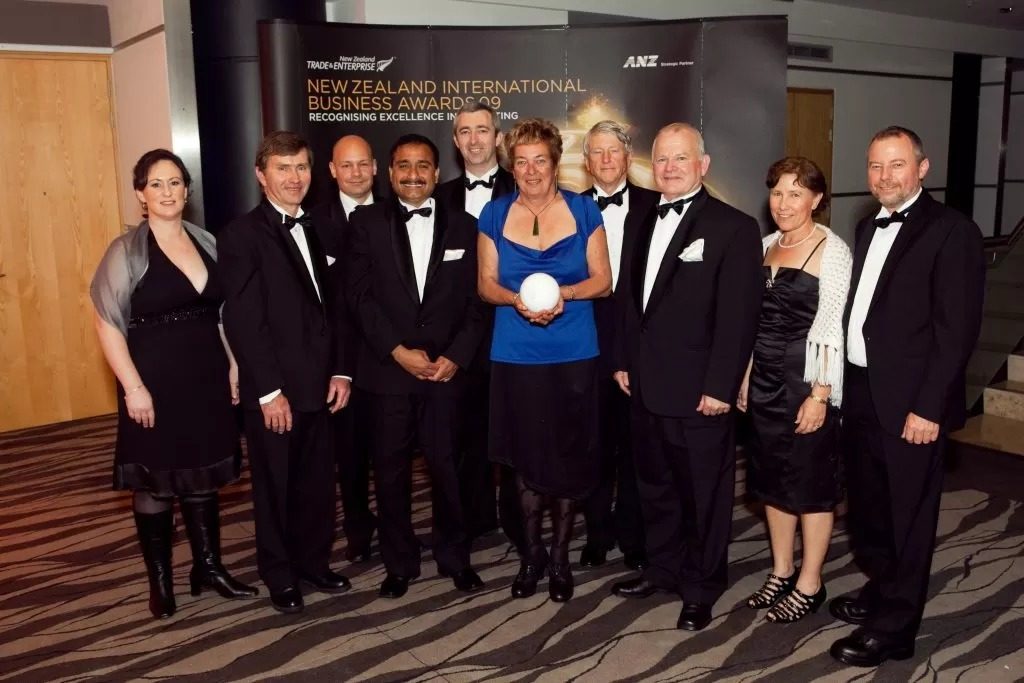
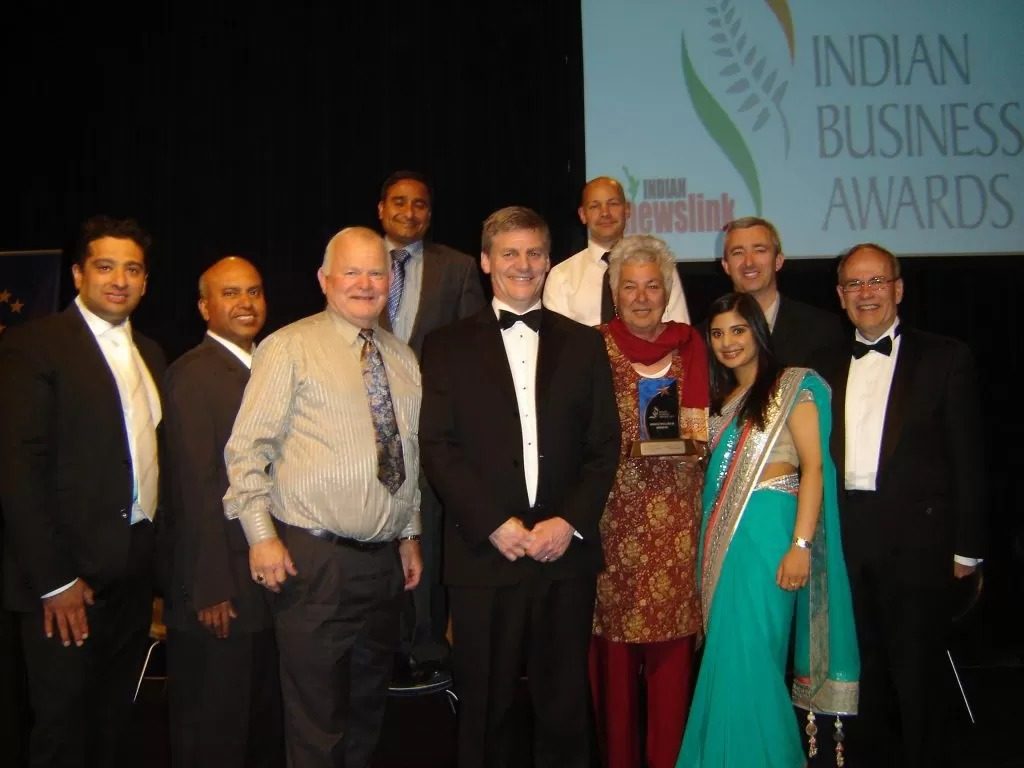
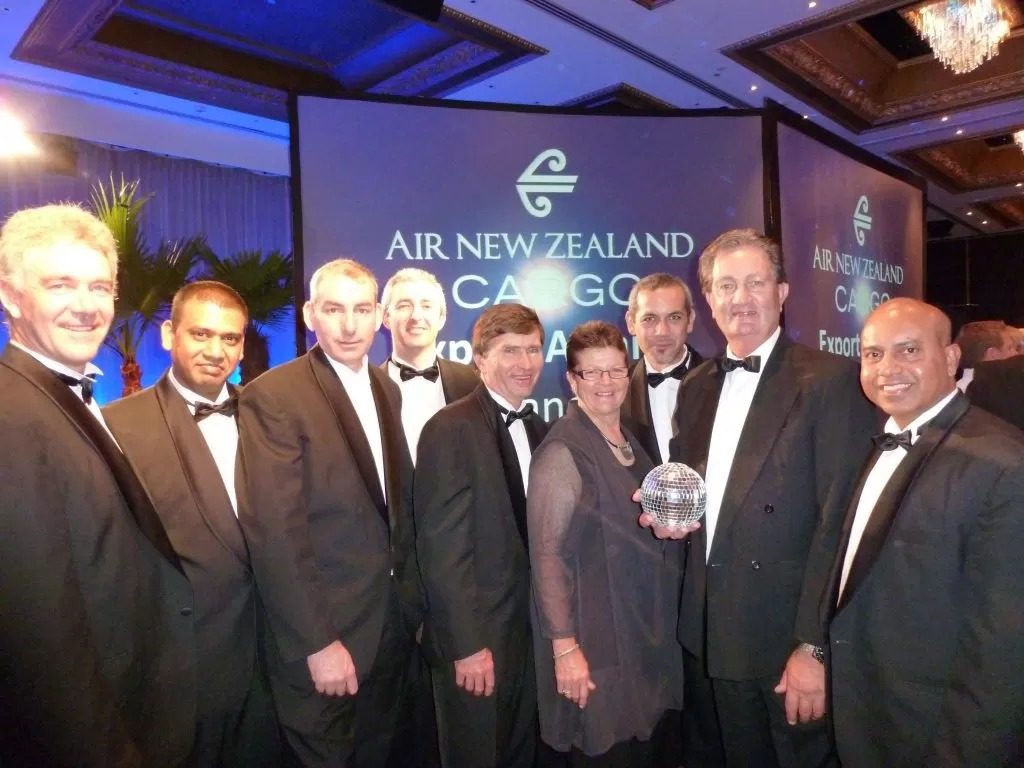
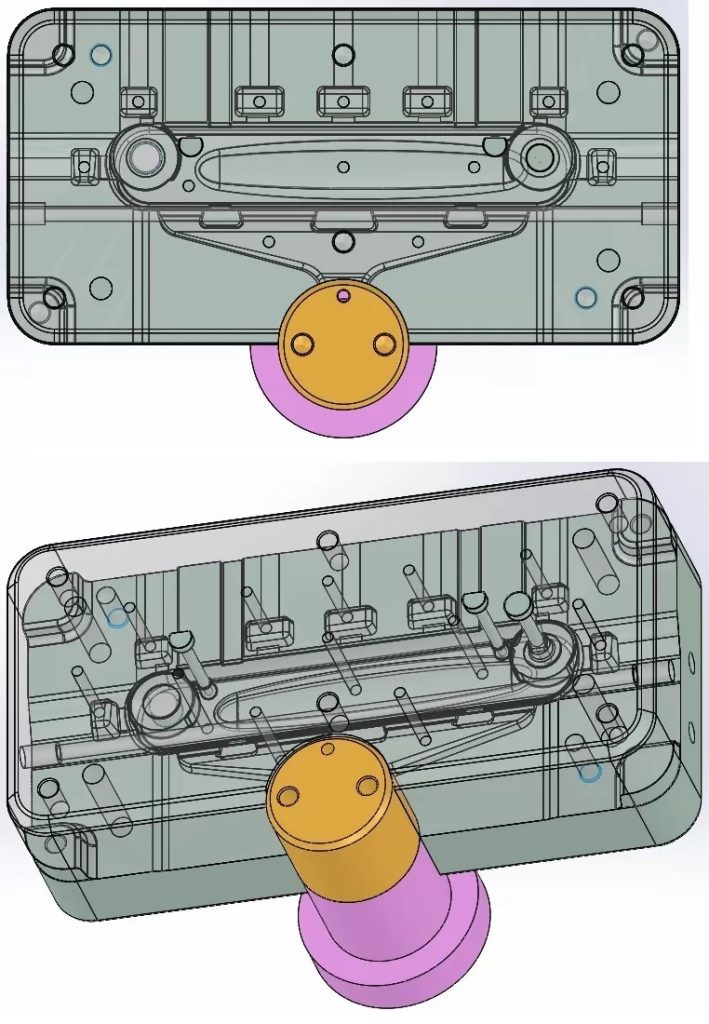